On this page: Template Download Instructions What is Root Cause Analysis?
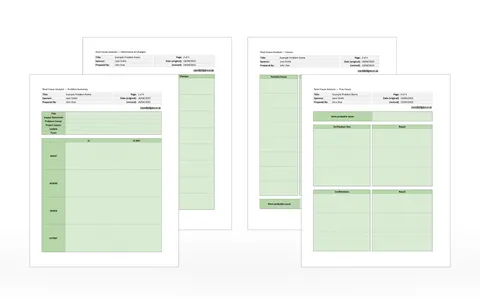
In this Template
- Root Cause Analysis (RCA) Template
- Beautifully formatted, easy to read.
- Example data included.
- Excel and Google Sheets formats.
- Ready to print: A4, U.S. Letter, etc.
- Comprehensive instructions and advice included.
How to Use This Template
Complete worksheets 1 to 4 of the spreadsheet in sequence using the following instructions.
To clear roadblocks, circle back and reconsider previous steps.
Worksheet 1
Fill in the Problem Summary
- Title
- A one line title — in the form of The Object and The Defect.
- Impact Statement
- Statement of the impact on the business and the goal.
- Problem Owner
- The Process Owner or Sponsor who is accountable for the problem.
- Project Leader
- The Black Belt or person responsible for the Root Cause Analysis.
- Update
- Date of last update.
- Team
- Build a team of subject matter experts from all functions involve.
Describe the Problem
- Interview team leaders and process owners who can add information and data to this detail descrption of the problem.
-
Add information to each of the categories below as it becomes available using the questions listed as prompts. The IS NOT categories may seem unnecessary but these can be particularly powerful.
- WHAT it IS
-
- What object or group of objects is having the problem?
- What is the defect or the nature of the problem?
- WHAT it IS NOT
-
- What object or group of objects could be having the problem but is not?
- What could be the defect or nature of the problem but is not?
- WHERE it IS
-
- Where geographically is the object when the problem is noticed?
- Where on the object is the defect located?
- WHERE it IS NOT
-
- Where geographically could the object be when the problem is noticed but is not?
- Where on the object could the defect be located but is not?
- WHEN it IS
-
- When was the prolem first noticed? What date? What time?
- When has the problem been noticed since then?
- Is there any pattern in the problem events?
- When in the history or life cycle of the object was the problem first noticed?
- WHEN it IS NOT
-
- When could the prolem have been noticed but was not?
- When could the problem have been noticed since but was not?
- When in the history or life cycle of the object could the problem have been noticed but was not?
- EXTENT IS
-
- How many units of the object have the problem?
- What is the size of a single defect?
- How many defects are there on any one unit?
- What is the trend in numbers?
- EXTENT IS NOT
-
- How many units of the object could have the problem but do not?
- What other sizes could be a defect but is not?
- How many defects could there be but are not?
- What could be the trend but is not?
Worksheet 2 — Develop Distinctions and Changes
- Distinctions
- What is different, or odd, or unusual or distinctive about each IS compared to the IS NOT?
- Changes
- What has changed in or around the timing of the problem? - Note the time or date of each change
Worksheet 3
Identify and Test Possible Causes
Develop possible causes
- Use the experience and knowledge of your subject matter experts to develop many ideas about possible causes.
- Use brainstorming rules, all ideas are good and should be retained.
- Use the distinctions and changes as useful triggers for brainstorming.
- List all possible cause statements.
- How does it explain the IS statements?
- How does it explain the IS NOT statements?
Does Not Explain
- List what is not explained.
Explains Only If
-
List "explained only if" conditions:
The IS or IS NOT statements that are explained — but only if something else happens or is present
Identify the Most Probable Cause
- Use the team's combined experience and logic.
- Consider rejecting the causes which do not explain key IS or IS NOT statements.
- Consider the probability of the only if condistions.
- Select the team's preferred cause statement and move to Step 4 to verify.
- If this fails to verify circle back to at least Step 3 and re-consider the next most probably cause.
Worksheet 4 — Verify the True Cause
- Design a test to demonstrate your understanding of the true casue.
- Verify that changing the input conditions will eliminate the problem.
- Confirm that removing the change will reinstate the problem.
- Verify removing the fix does reinstate the problem.
Additional Final Steps
- Develop the permanent fix changing the process to prevent reoccurence.
- Record and archive the results of the problem analysis and the findings.
- Record in project documentation or SOP the change in process.
- Include a lessons learned review and identify similar issues or opportunities to use Root Cause Analysis
What is Root Cause Analysis?
RCA is an advanced problem solving technique for when simpler techniques such as The Five Whys won’t solve it.
If you have a broken complex machine or manufacturing process with an unknown root cause you will need a systematic and analytical approach to problem solving.
This technique is not unlike the differential diagnostic process used by a doctor when confronted by many conflicting symptoms and no obvious cause.
Doctors will collect as much information as they can, consider all possibilities, then by ruling out those that don’t fit the facts, they identify the most likely cause. Before recommending treatment they will likely propose a diagnostic test to confirm the condition.
This is exactly how we approach a Root Cause Analysis to find the true cause of the fault.
- Specify the problem and collect all of the known facts or observations.
- Identify what is distinctive and also what has changed in the timeline.
- Brainstorm all possible causes suggested by those distinctions and changes. Then go on to test which possible cause best fits the facts.
- Design a diagnostic test to verify the one true cause
And if at first you don’t succeed, circle back to gather more observations, more possible causes and repeat the testing process.
Find out how Root Cause Analysis can help your organisation.
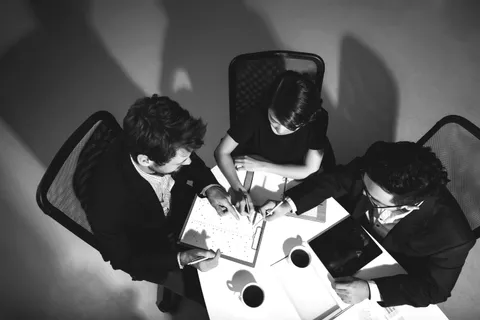
Free: Lean Six Sigma
Project Template Library
Sign-up for email updates and get:
- Unlimited template library access.
- Microsoft Excel and Google Docs template files.
Plus:
- Subscriber-only course discounts
- Unlimited Free consultation with our Master Black Belt.
- Regular updates, including new articles and free resources.
This site is protected by reCAPTCHA and the Google Privacy Policy and Terms of Service apply.